단조소입의 냉각과정에 따른 문제
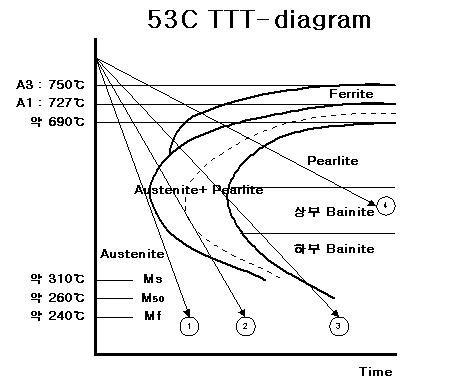
1. 53C의 경우 아공석강이므로 상태도 상에서 Austenite+Ferrite 구간이 존재하여
위의 TTT-diagram과 같이 초석 Ferrite가 나타나는 구간이 존재함.
2. 따라서 A3선 이상의 온도에서 서냉(로냉등)시 초석 Ferrite 구간을 통과하게 되어
입계에서부터 초석 페라이트가 발생됨.
3. 단, 단조소입의 경우 1050℃이상에서는 조직의 조대화가 급격하게 일어나므로
좀 더 냉각이 빠를 경우(공냉, 느린유냉등), 성장하는 초석 Ferrite 입도에 비해
비교적 큰 Austente의 입도에 의해 냉각 도중 Austenite 중심은 Ferrite에 대해
과포화 되어 이런 과포화 현상을 없애기 위해 초석 Ferrite가 활성화에너지가
큰 Austenite 결정립 안에서 핵생성하고 성장함.
따라서, 입계에 나타나는 초석 Ferrite의 양은 줄어드는 반면 Widmanstatten 판이
Austenite 입내에 나타남. * Normalizing을 통해 Widmanstatten 조직을 없앨 수 있음.
4. 구상화 Annealing은 Ferrite와 Cementie(Fe3C)로 구성된 Pearlite 조직을 A1점 직하의
온도에서 장시간 유지시켜(아공석강의 경우) 탄화물(Cementie(Fe3C))을 구상화시키고
기지는 Ferrite조직으로 분리시켜 기계가공성등을 증대시키는 열처리 방법임.
5. 재질별 기계가공성을 증대시키기 위한 열처리 방법
45C 이하 : 저온풀림 (670℃, 공냉)
45C ~ 50C : 완전풀림 (850℃, 로냉)
53C 이상 : 구상화풀림 (700℃, 로냉)
SCM3 : 완전풀림 (850℃, 로냉)
단조 소입
1. 조건
1) 강종 : 탄소강이 적용
합금강의 경우는 단조소입이 경화능이 너무 좋아져 크랙발생우려
2) 단조 온도 : 1200~1300℃
단조 소입온도 : 1100~1200℃
3) 설비 : 드롭해머는 단조소입온도가 부정확하고 경화가 균일하지 않기 때문에 프레스
단조가 효과적이며 유조는 균일한 냉각이 이루어지도록 연속식으로 하며 트리밍 프레스에 직결되어 있고 또 유냉이 완료되면 곧바로 템퍼링 할 수 있도록 템퍼링 로가 연결되어야 함.
* 유조의 경우 화재위험이 있을수 있으므로 PGA폴리머와 같은 수용성 경화제사용
2. 적용 및 잇점
구조용 중탄소강의 경우 경화능이 적기 때문에 유조에 소입시 불완전한 담금질 조직이 되어 뜨임 후에도 인성이 낮아서 부품을 크게 만들거나 혹은 합금강으로 대체하는 예가 많았으며 절삭성이 불량하여 후가공에서 생산성 저하의 요인이 됨. 이에 반해 단조품을 자열을 이용하여 담금질 하는 방법은 경화조직과 인성 및 절삭성이 개선되어 저급재질의 활용이 넓어지고 에너지 절약에 의한 경비절감에 도움이 됨.
3. 단조소입의 적용 및 기계적 성질
1) 탈탄깊이 : 단조가열온도 1100~1200℃ - 0.5mm
온도증가에 따라 1200~1300℃ - 1~3mm
1350℃ 이상에서는 처음에는 급격히 산화막이 형성되어 탈탄이 빠르게 진행되나
산화막이 안정화되면서(Fe-O diagram 참조) 탈탄이 지연됨 - 0.5mm
2) 경화능 : 재가열하는 QT에 비해 단조소입은 산화막이 얇아 냉각제가 표면에 직접 닿
을 수 있어 냉각이 빠르고 높은 오스테나이트화 온도로 인하여 결정립이 조대화
되어 경화능이 증가되므로 심부까지 마르텐사이트로 변태되는 유효경화 깊이가
증가됨.
3) 경도 : 정상 소입 경도로 소려온도 상승에 따른 경도 균일.
4) 충격치 : 오스테나이트 입자는 조대하나 충분한 소입이 확보되므로 충격치가 약 1.4배
정도 상승 - 인성은 입도의 영향은 간접적이고 입계의 석출물 및 입도 성장에
의해 생기는 각종원소의 고용 또는 석출에 주로 관계됨.
5) 인장강도 : 소려온도 상승에 따른 소려경도 균일로 인장강도 균일.
6) 피삭성 : 균일한 솔바이트로 피삭성이 월등하게 좋음 (가공라인 특성상 다소 차이)
7) 일반 QT 제품의 경우 불완전 소입으로 초석페라이트가 석출될 우려가 있으나 조대
오스테나이트 입자에 의한 변태속도 지연과 냉각시 스케일이 없어 급냉효과로 인해
초석페라이트가 없슴.
1. 합금강(SCM4)의 단조소입에 따른 문제
1) 연소 : 강을 대기중에서 고상선이상의 온도로 가열하면 석출물이나 불순물들이 편석하기 쉬운 결정 입계를 따라 용융이 시작되고 용융된 입계를 통하여 산소가 침입하므로서 산화물이 발생한다. 제강시 산소가 침투하여 발생한 산화물은 주로 저탄소강에서 Wustite로 존재하며 용융점은 1370℃~1430℃사이에 존재한다. 산화물발생을 유발하는 산소는 제강시 뿐만 아니라 단소시 고온에 의하여 결정입계로 확산이 되어 들어가게 되며 재료의 편석 및 재료의 소성유동에 의하여 온도가 상승하는 것, 산화에 의하여 발열하는 것 등으로 인하여 가열온도가 평균화학조성에 비해 고상선 이하의 상당히 낮은 온도에서도 산화물이 발생하여 국부적인 균열을 일으키게 되어 담금질 균열의 원인이 된다.
2) 과열 : 강을 장시간 1000℃이상의 고온에서 유지하게되면 입자가 조대해지고 고온에서 담금질시 냉각속도가 증가되면 Martensite 조직은 큰 침상형태로 나타나게 되며 내부 조직의 응력이 원인이 되어 이 마르텐사이트 조직은 절상으로 미세하게 파괴되게 된다. 마르텐사이트 조직이 파괴되면서 생긴 작은 균열은 큰 균열의 시발점이 될 수 있다. 따라서 소입성이 좋은 강은 과열될 경우 더욱 위험하다.
3) 질량효과 : 두께에 따라 다르나 소입성이 좋은 강일 경우 내부까지 깊이 경화되어 표면층에 인장응력이 발생하게 되어 담금질 균열의 위험성이 높다. 반면 소입성이 좋지 않을 경우 외층만이 마르텐사이트로 팽창하기 때문에 압축잔류응력이 생겨 담금질 균열의 위험성이 적다.
4) 잔류오스테나이트 : 만일 유냉등으로 Ms~Mf구간을 천천히 통과하게 되면 잔류 오스테나이트가 더욱더 많이 발생하며 이 잔류오스테나이트의 발생으로 담금질시 유심 담금질이 되게 되어 담금질 균열이 일어날 확률이 적다. 그러나 담금질 상태 그대로 두게 되면 이 잔류 오스테나이트는 시간이 경과함에 따라 마르텐사이트로 변태되어 팽창되므로 응력발생의 원인이 되어 시효균열의 원인이 된다. 따라서 담금질 후 잔류오스테나이트를 안정화 시키기 위하여 심냉처리를 하거나 탄소강이나 저합금강의 경우 250℃~350℃이상에서 템퍼링하여 베이나이트 및 그 이외의 조직으로 분해하여야 시효균열을 방지할 수 있다. 시효균열은 특히 상온이하로 냉각시켰을 때 추운 겨울날 밤에 주로 많이 발생한다. 시효균열을 방지하기 위한 템퍼링은 3시간 이내에 담금질 후 60℃이하의 온도로 냉각시킨 후 하며 너무 빠르면 뜨임처리가 되지 않으므로 주의를 해야 한다. 그날 중 뜨임처리가 되지 않으면 100℃이상의 탕속에 뜨임처리를 하고 다음날은 정상적인 뜨임처리를 해야한다.
5) 기타 : Metal Flow에 의한 접힘(folding), 플래쉬의 접힘등..
6) 형상 : 단면의 급변부, 예리한 모서리, notch부분, 구멍, 파팅 라인부분이 균열의 위험성이 높다.
-----------------------------------------------
첫댓글 달빛님! 오랜만입니다. 반갑구요. 좋은 자료 남겨 놓으셨군요. 감사합니다. 회원님들께 많은 도움이 되리라 믿습니다.