UV LED란 웨이퍼 위에 약100 미크론 두께의 GaN 칩을 에피 성장시킨 칩을 팩캐징하여 집광 시스템과 방열을 극대화 한 uv led칩 모듈이다. 전력이 인가되면 1-8%가 uv에너지로 방사되며, 80% 이상이 열에너지로 방사된다.
1), LED개발 역사 가.1962년 GE가 GaAsP를 이용한 적색 LED를 발명했으며, 1968년부터 양산함. 나. 1980년대에는 AlGaAs 기술을 이용한 고휘도 적색 LED가 개발되면서 sign, signal, display 분야로 응용되기 시작됨. 다, 1 9 9 2년 InGaAlP 기술을 이용한 초고휘도 적색 LED가 개발되면서 교통신호등, 자동차 램프 등으로 활용되기 시작함.
라. 질화물 반도체는 1986년 일본의 아카사키 교수가 AlN 버퍼층을 이용하여 고품위 GaN 결정을 성장시켜 Mg 도핑후 LEEBI (low-energy electron beam irradiation) 후처리를 이용하여 2×1 01 6c m- 3 의 정공 농도를 얻은 결과를 바탕으로 1991년에 p-n 접합식의 GaN LED 개발. 마. 1993년에는 니치아의 나카무라 슈지 박사가 저온에서 성장된 GaN 버퍼를 사용하여 양질의 질화물계 박막을 성장하였고, 그 후 InGaN/GaN 다중양자 우물층을 활성층으로 한 고휘도 청색 LED가 개발됨. 바. 2000년 InGaAlP 적색 LED 방사효율이 100 lm/W를 기록하면서 형광등(80 lm/W)을 능가하는 효율을 보임. - 2000년 전후로 RGB 및 백색 L E D의 효율과 출력이 빠른 속도로 증가하면서 휴대용 단말기 LCD 백라이트, 자동차, 전광판, 특수 조명분야 등 응용범위가 넓어지기 시작함
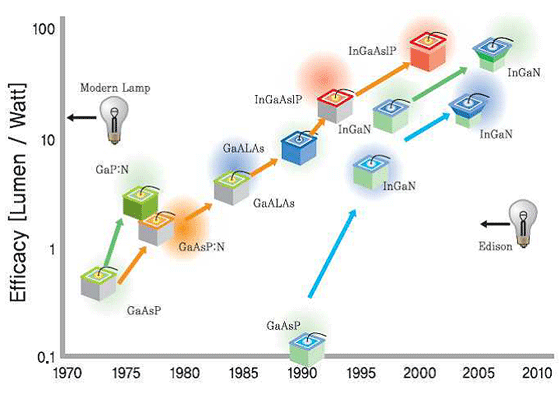
LED발전역사
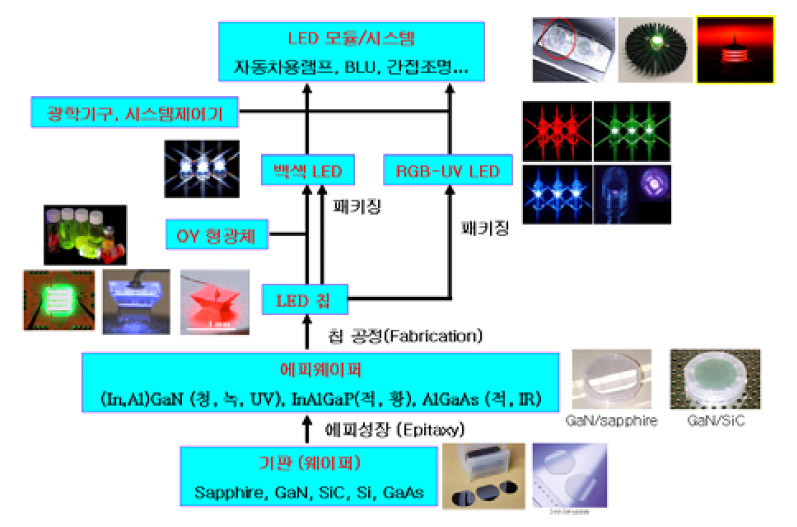 LED 램프계열
2). UV LED의 특징
|
- 0 .3 mm ~ 2 mm의 소형 칩을 사용하고 지향성 광원이므로 부품 및 모듈의 슬림화가 가능 - 수십나노( ~ 1 0- 8)초 단위의 고속응답 속도를 가지므로 on-off 스위칭이 램프에 비해 매우 빠름 - 초기 출력 대비 50% 감소시점을 수명으로 볼 때 일반 사용조건에서 GaN 계열 LED는 10만 시간, GaAs 계 LED는 100만 시간으로 수명이 길다. - 스펙트럼의 선폭이 작으므로 색순도가 좋고 고속변조가 가능하다 - 칩에서 방사되는 파장과 광출력이 칩 온도에 매우 민감하다. | 온도에 따른 파장변화 및 광출력 변화가 큰 것은 고출력 램프나 UV LED 경화기에 매우 큰 걸림돌이며, 이를 해결하는 것이 led 연구자의 가장 큰 목표이다.
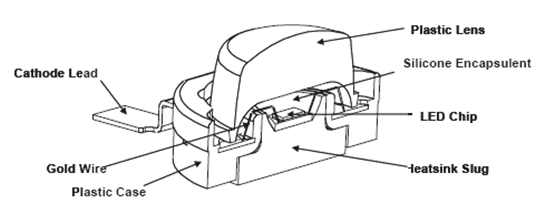
3). 고효율및 고출력 UV LED 개발 포인트 (이 부분은 LED 기부터 팩키징 까지의 LED 의 효율을 높이고 생산성을 올리는 데 관련된 자료이므로 LED 칩 개발 엔지니어가 아니라면 읽을 필요는 없다)
가. 기판 ○ LED 기판용 재료는 GaN LED의 경우 Sapphire, SiC, GaN, Si 등이 사용되며, 단가 문제 등으로 인해 주로 Sapphire 기판을 사용하며 Cree에서는 SiC 기판을 사용하기도 함.( InGaAlP 및 AlGaAs 계열 LED는 GaAs 기판을 사용함). ○ GaN 기판은 격자부정합이 없는 동종 기판이어서 결함제어가 용이하지만 고가이고 수율이 낮다.. ○ Si 기판은 저렴하고 대형기판 적용이 가능하기 때문에 저가격화에 가장 유리하며 열 방출에도 용이하여 몇몇 기업에서 시도하고 있지만 격자부정합이 크고 Sapphire에 비해 soft한 재료이기 때문에 결함제어가 어렵고 동작전압이 높다는 단점이 있다.
나. 에피택시 성장(Epitaxy) ○ LED 기본 성장구조
|
- 기판위에 LED 구조는 MOCVD (metal organic chemical vapor deposition)로 성장시키며 50 um이상의 후막층 (thick film)은 HVPE(hydride vapor phase epitaxy)로 성장시킨다. - GaAs 기판을 이용한 InGaAlP계 LED는 격자정합 구조이므로 결함의 생성이 문제가 안되지만 Sapphire 기판과 질화물계 에피층의 격자 부정합도는 매우 크므로 근본적으로 결함없는 에피층의 성장이 불가능하다. - 질화물계 LED 에서 전위(dislocation) 같은 결함의 생성을 최소화하고 결함의 전파를 억제하기 위해 기본적으로 적용하는 기술은 저온 버퍼층 성장기술로서, 500℃ 부근의 저온에서 AlGaN (0≤×≤1) 핵 생성층 (nucleation layer)을 20-30 nm로 얇게 형성한 후 온도를 올려 스스로 단결정화 시키는 방법을 사용하고 있다. - 버퍼층 위에 순차적으로 n -층, 활성층, p-층의 구조를 성장시키며 보통 p -전극과의 접촉저항 을 낮추기 위해 p -층위에 고농도로 도핑된 p+ 층을 성장시킴. 완성된 LED 기본 에피구조는 아래 그림과 같다 . - 활성층으로는 효율을 높이기 위해 보편적으로 다중양자 우물구조 (Multi quantum well, MQW)를 삽입하는데 원하는 파장을 얻기 위해 우물층과 장벽층의 조성 및 두께를 제어한다. |
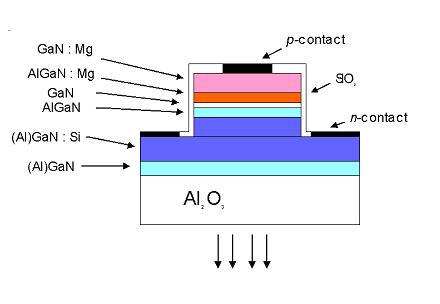 [ 질화물계 LED 기본 구조 ]
|
- 도핑 원료로는 n-형의 경우 Si이 가장 많이 사용되며 p-형의 경우 InGaAl P계 재료에서는 Zn, 질화물계에서는 Mg이 사용되는데 M g의 활성화가 충분치 않아 p층 저항이 높은 문제가 있음. - 이는 성장분위기 중의 수소가 억셉터 도핑 물질인 Mg과 결합하여 Mg-H 복합체를 형성하며 전기적으로 compensation된 결정이 성장되기 때문인데 Mg-H 결합을 끊어주기 위해 아카사 키 교수에 의해 LEEBI 방법이 처음 시도됐었고 후에 나카무라 박사에 의해 시도된 고온 열처 리 방법으로도 충분히 효과를 보게 됨. - AlGaN/GaN 계열의 재료는 기판과의 큰 격자부정합도 이외에 열팽창계수 차가 크므로 높은 Al 조성 및 두꺼운 박막층을 성장할 경우 crack이 발생할 수 있으므로 임계두께의 제어와 초격 자 구조를 이용한 완충층의 활용이 필요함. |
다. GaInN 에피층(epitaxy layer) 성장
|
- GaInN의 에너지 밴드 갭 값 0.7 eV (1771 nm)로 매우 작음. - 이는 InXG a1 - XN ( 0≤×≤1 )의 에너지 갭이 적외선 영역에서 자외선 영역을 방사하는 것을 의미하며 양질의 GaInN 구현이 가능하다면, 질화물 반도체만으로 좋은UV LED 제작이 가능함 - 그러나 Ga N에서 In의 인입이 많아지거나, InN에서 Ga의 인입이 많을수록 상분리 현상이 심 하며 이를 막기 위해 성장온도를 높이게 되면 In dissociation이 생겨서 양질의 막을 생산하기 어려움. |
라. 양자점(Quantum dot) 구조 성장
|
- GaN/AlN 양자점의 경우 이들의 격자상수 차이는 3% 정도로서 그동안 III-V 화합물반도체의 양자점 연구에서의 격자상수 차이와 유사하기 때문에 많은 그룹에서 연구되고 있음 - InGaN 양자점의 경우 양자점에 의한 효과라기보다는 InGaN 구조 자체가 상분리 및 In 조성 불균일성으로 인해 생기는 carrier localization 때문에 발광효율이 증가한다는 것으로 알려짐. - 양자점의 크기를 조절하여 발광파장의 제어가 가능하므로 RGB를 모두 발광하는 양자점을 다중구조로 성장하여 백색광을 낼수도 있음. |
마. 측면 에피택시 성장
|
- Epitaxial lateral overgrowth (ELO) 기술은 1980년 중반 integrated circuits (IC) 제조를 위한 Si의 ELO 기술에서부터 시작됨. - 1 9 8 0년대 후반부터 opto-electric integrated circuits (OEIC) 제조를 위해 LPE, MOCVD, MBE 등을 이용한 GaAs, GaP, InP 등의 ELO 기술이 발달하였고, 1990년대 후반 단파장 LED , LD 및 고출력, 고주파 전기소자 제조를 위해 MOCVD, HVPE 등을 이용한 G a N의 ELO 기 술이 개발됨. - 질화물반도체에는 1997년 GaN/SiC의 결정성 향상을 위해 처음 적용됨 - 이 기술에선 GaN 박막이 sapphire, Si, SiC 등의 이종물질 기판 위에서 마스크 및 기판의 패 턴에 따라서 선택적으로 수직, 수평 성장하고, 수평성장 영역에서 threading dislocation (TD)은 bending되거나 mask에 의해 차단됨으로써 표면으로의 침투가 억제됨. - 이런 특성을 이용하여, SiO2를 PECVD로 증착한 후 mask를 patterning하고 그 위에 GaN을 MOCVD 성장하면 window 영역 (혹은 seed 영역)으로부터 성장되는 GaN는 SiO2 mask 쪽 으로 측면성장하고 SiO2 mask 상의 GaN는 전위를 거의 포함하지 않는 고품위의 결정성을 가짐. |
|
- wing 영역에서 TD density는 대략 ~ 106 cm- 2 의 값을 가지며 window 부분에 비해 10,000배 감소한 것임. 성장 변수를 조절하여 측면 성장 속도를 수직 성장속도의 2배 이상까지 증가시킬 수 있음. 1997년 나카무라 박사에 의해 ELO GaN 기판위에 InGaN-based short- wavelength LD가 제작됨으로써 GaN 물질의 ELO 기술은 단파장 LD의 효율을 위해 더욱 발전. - Pendeo-Epitaxy (PE), Cantilever Epitaxy (CE), Lateral Epitaxy on Patterned Sapphire (LEPS) 등의 기술도 모두 수평 성장을 통하여 TD 표면침투를 억제 시키는 기술로 ELO 기술 에서 변형된 것들임. - Pendeo epitaxy는 maskless ELO라고도 불리우며, 2001년R.F.Davis 그룹에서 처음 연구 결 과를 보고함 - GaN을 Sapphire 기판 위에 성장한 후, 기판까지 건식 식각하여 기판을 patterning하고 그 위 에 다시 GaN을 성장하면, 노출된 기판 위에는 성장이 되지 않고 GaN 위의 성장이 우세하게 됨. 성장 변수를 조절하여 측면 성장 속도를 수직 성장속도의 2배 이상까지 증가시킬 수 있으 며, SiO2 등의 mask를 사용하지 않는 특징이 있음. - FIELO (Facet-initiated ELO) 기술은 1997년 Usui 등에 의해 개발된 HVPE를 이용한 측면 성 장 방법으로서, ELO와 같이 GaN<1-100> 방향의 SiO2 mask를 채용. 성장조건을 조절하여 처음에 facet을 만들고 HVPE 법을 이용하여 GaN을 두껍게 성장하여 표면을 평활한다 |
Pendeo Epitaxy
|
- 이 방법은 수평성장 부분인 mask 영역은 물론 수직 성장 부분인 window 영역에서 TD density를 감소시킬 수있는 장점을 가짐. - FACELO (Facet-controlled ELO)는 2000년 일본 Mie 대학의 Hiramatsu 교수팀과 Sumitomo Corporation에서 공동 개발된 기술이며, MOCVD 법으로 서로 다른 성장조건에서 2-step ELO 성장하는 방법임 - ELO와 같이 GaN<1-100> 방향의 SiO2 mask를 만들고, 그 위에 성장조건을 저온(혹은 고압 )으로 조절하여 facet을 활성화시킨 후, 고온(혹은 저압)의 다른 성장 조건으로 facet을 활성화 시켜 표면을 평탄화시키는 방법. FIELO에서는 HVPE를 이용하여 두껍게 GaN을 두껍게 성장 하는 방법으로 표면을 평탄화하였으나 FACELO에서는 MOCVD 성장 조건을 다르게 하여 얇 은 GaN 박막에서 탄화시킨다는 점이 다름. - Hiramatsu 등은 FACELO 기술을 이용하여 GaN 박막전 영역에서 TD density를 106 cm2대로 줄일 수 있고, 마스크영역 GaN <0001>축의 tilt를 undoped GaN의 tilt 수준으로 줄일 수 있다 고 보고함 - University of California at Santa Barbara의 DenBaars 그룹에서는 2 0 0 1년 ELO 기술에서 부터 응용되어 개발된 cantilever epitaxy (CE) 기술을 이용하여 SiC 기판과 Si 기판 위에 GaN 박막을 선택적으로 수직, 수평 성장함 - CE 기술이 ELO 기술과 다른 점은 패턴공정 전에 GaN seed 층을 성장 하지 않는다는 것임. 이 기술에서는 SiC기판이나 Si 기판을 stripe 패턴으로 수 μm까지 에칭한 다음 기판 stripe의 top plane에서 수직 성장된 GaN를 기판의 trench 위로 수평 성장 시키는 방법임. 기판 stripe의 top plane에서 GaN 박막이 성장될 때 trench에서도 GaN이 성장되는데 기판 trench에서 성장된 GaN는 stripe의 높이까지 도달하기 전에 stripe의 top plane에서 성장된 GaN의 수평성장에 의해 덮어지게 됨. - Katona 등은 Si 기판과 SiC 기판 위에 CE GaN을 성장하여 AFM image에서 나타나는 dartk pit density를 계산한 결과 stripe의 ltrench 영역에서 CE GaN/SiC의 경우 9×108cm2을 보고 하였고, CE GaN/Si(111)의 경우 7.5×109 cm2였고, wing 영역에서는 두 경우 모두 dark pit이 관찰되지 않았다고 보고함 . - 또한 이 기술에선 TD의 침투를 막기 위한 dielectric mask를 사용하지 않지만 0.8도 이하의 wing tilt가 관찰된다고 보고함. |
바. 칩제조 공정(Fabrication)
|
- LED 칩을 제작하기 위해서는 패턴 형성을 위한 노광(photolithography), 식각(etching), 금속 전극 증착(metallization), Passivation, lapping/polishing 등의 단위 공정을 거쳐 0.3×0.3× 0.1mm 정도의 칩으로 분리되는데 적절한 공정방법을 통해 광추출 효율을 크게 개선할수 있음 - GaAs를 사용하는 InGaAlP계 LED는 기판이 전도성이므로 전극은 top-bottom의 형태로 제작 되지만 Sapphire 기판을 사용하는 경우, 기판이 절연체이므로 전극을 형성하기 위해 n - GaN을 일부 식각(mesa etching)하여 top-top 방법으로 전극을 배치. - p -층의 저항이 높을 경우 p 층에서의 수평방향 전류흐름을 원활하게 하기 위하여 전극금속과 p -층 사이에 5 - 7nm 두께의 얇은 금속막을 입혀 투명전극으로 활용함. - 최근에는 얇은 금속 투명전극대신 비금속 산화막을 이용한 투명전극을 사용하여 광 투과율을 90% 이상까지 높일 수 있지만 접촉저항이 높아 작동전압이 증가된다는 문제가 있음. |
사. 플립칩(flip chip) 공정
|
- 빛의 추출 효율(extraction efficiency)을 살펴보면, 기존 발광소자는 위쪽으로 빛이 방출되므 로 빛이 발광층에서 나오는 동안 투명 금속이나 결합 패드(bonding pad), 전극 연결부에 의해 흡수되어 빛의 손실이 큼. - 따라서, 고출력의 발광소자를 만들기 위해서는 소자의 크기가 커져야 하지만, 수직으로 빛을 내는 방식에서는 p -GaN의 높은 저항으로 인해 전류 퍼짐이 좋지 않아서 소자 전체가 발광에 기여하지 못하게 되므로 소자의 크기에 한계가 존재함. 또한, 고출력 L E D를 제작하기 위해서 는 발광 효율, 소자 크기, 열저항 등을 다각적으로 고려해야 함. - 이런 조건을 고려하여 플립칩(flip-chip) 방식의 발광소자가 개발. 플립칩 방식을 이용한 발광 소자는 기판인 Sapphire를 통해 빛이 방출 - 플립칩 방식에서는 S a p p h i r e쪽으로 빛을 나오게 함으로써 금속 접촉부나 결합 패드, 전 극 연결부에서의 손실을 최대한 줄일 수 있음. 또한 두꺼운 p - metal을 사용하여 전류퍼짐 현상이 좋아지게 되어 낮은 순방향 전압을 제공하고, p-GaN 위에 반사율이 좋은 금속을 삽입 함으로써 빛을 S a p p h i r e쪽으로 대부분 반사시켜 광추출효율을 향상시킴. - 고출력 발광 소자의 경우 주입 전류가 커질 때 많은 열이 발생함. 기존의 위쪽으로 빛을 내는 방식의 발광소자 에서는 열저항이 200℃/W에 달함. - 플립칩 구조에서는 두꺼운 p 금속을 이용하는데 열발생 지역인 활성층으로부터 p금속까지의 거리가 가까우므로 방열이 용이하고 좋은 방열재료를 이용하여 열저항을 크게 감소시킬수 있음. 현재 열저항의 최저 수준은 8℃/W임 (Lumileds 사의 Luxeon 모델) . - 이 구조에서는 Solder ball의 역할이 중요하여 solder ball 형성법, 균일성, 열전도도등이 성능과 생산성을 좌우하는 요소가 됨. |
아. 추출효율 개선 - 칩 내부에서 발생한 광자는 밖으로 빠져나오는 동안 결함에 잡혀 열에너지로 변환되기도 하고 전반사(internal total reflection)에 의해 안에서 travelling 하다가 소멸되는 손실이 크기 때문에 공정을 통하여 이를 최소화 할 필요가 있음. - 전반사 현상은 칩의 구조학상 정육면체 칩일 경우 칩 내부의 굴절율과 외부환경의 굴절율 차이가 있을 때 칩과 외부매질 사이의 경계면에서 반사가 생기는데 특정한 반사각 이상에서는 100% 반사되는 현상임. - 이러한 현상으로 인해 현재 일반 LED 의 광추출효율을 계산해보면 10% 정도에 불과하며 이를 올리는 것이 가장 큰 관건이다.
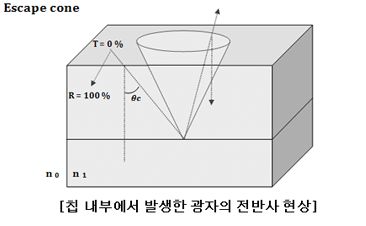
- 표면에서의 전반사를 줄이는 방법으로는 표면에 도달한 광자가 랜덤하게 scattering 되도록 표면 패턴을 형성하는 방법(fixture), 칩의 모양을 절두형 역피라미드형으로 제작하는 방법(TIP, truncated inverted pyramid 또는 ATON과 그의 플립칩 NOTA) 등이 있으며 최근에는 특정파장의 광자만 선택적으로 투과 또는 반사시키도록 LED 표면에 광자결정 (photonic crystal)을 패터닝하는 방법이 시도되고 있음. - 기판을 떼어내고 열전도율이 좋은 금속기판으로 재부착하는 방법( Thin GaN)이 현재는 가장 좋은 추출효율이 72%로 가장 높음. - 대면적 칩은 보통 1×1mm 이상의 칩을 말하며 칩의 크기가 증가하면 전극간의 거리가 멀어지면서 p -층 정공의 확산이 어려워지는 현상이 생기므로 전극 배치를 아래 그림처럼 다양하게 배열 함 (finger cell 또는 multi parallel cell 등) .
자. 패키징(Packaging) 칩을 모듈이나 시스템에 응용 가능하도록 패키지 공정을 거친다, 패키지의 목적은 칩을 외부로부터 환경적, 기계적, 화학적, 전기적으로 보호해 주는 역할 뿐만 아니라, 광추출효율 향상, 열방출 매개체로서의 역할도 매우 중요하다. ○ 응용 제품이 다양하고 표준규격이 없기 때문에 매우 많은 종류의 패키지 형태가 있으나 대표적으로 램프형, SMD(surface mount device), COB(chip on board), BLU(backlight unit)가 있다. ○ 패키지 기술의 방향은 응용제품에 따라 초박화(side view BLU), 소형화(top view BLU), 고출력화(조명)로 진행되고 있다(니치아 패키지 로드맵) . ○ 패키지 과정에서 고려되어야 할 사항은 mount의 열전도성, 에폭시 수지의 내열성, 내자외성 등이며 고출력 LED로 갈수록 이러한 문제가 심각해진다. ○ Lumileds사의 1-5 W급 LED는 이러한 조건을 잘 만족시켜주는 제품이다.
|