|
중국 상하이 대우버스 생산공장.

32개국 63개 현지법인을 두고 지게차와 버스를 생산하는 영안모자가 최근 계열 내 국내외 생산직 근로자의 임금과 노동시간을 비교한 결과, 한국 근로자의 임금이 미국과 독일에 비해 각각 56.3%, 27.3% 높은 것으로 나타났다.(지난해 기준 한국 6만2691달러, 미국 4만112달러, 독일 4만9250달러) 반면 연간 근로일수는 이들 선진국에 비해 10일 정도 적었다.(한국 242일, 미국 251일, 독일 250일)
멕시코·베트남 등과 견줘봐도 사정은 같았다. 지난해 1인당 GDP(국내총생산)가 우리의 44% 수준인 멕시코 공장 근로자의 임금은 우리의 9% 수준에 불과했고, 한국처럼 주5일제를 실시하고 있는데도 멕시코 근로자들은 한국보다 연간 12일을 더 일했다. 베트남 공장 근로자들은 한국의 9% 수준의 임금을 받고 연간 58일을 더 일하는 것으로 나타났다.
한국의 추락하는 제조업 생산성과 관련, 특정 업체가 국내외 사업장을 비교한 자료를 공개한 것은 이번이 처음이다. 영안모자 백성학 회장은 “한국의 제조업은 고비용이어서 이대로 가면 해외로 다 이전할 수밖에 없다”며 “이번 조사 자료를 국내 생산성이 왜 추락했는지를 분석하는 참고자료로 활용해 달라”고 말했다.
◇미국·독일 보다 임금은 56~27% 더 많이 받으면서 근로일수는 연간 10일 정도 적은 한국 근로자들
1959년 서울 청계천에서 모자를 생산해 파는 구멍가게로 출발한 영안모자는 지난해 연매출 2조5300억원을 올렸다. 연간 1억개의 모자를 생산, 전 세계 모자 시장의 40%를 차지한다. 현재 대우버스와 지게차를 생산하는 클라크(CLARK), 자일자동차판매, OBS(경인방송)를 계열사로 두고 있다.
기업의 모태(母胎)인 모자 제조는 1993년 국내 생산을 중단하고 생산 라인을 전부 해외로 이전했다. 영안모자의 조사 자료에서 가장 눈에 띄는 것은 국내외 근로자 간의 임금 격차이다.
미국은 1인당 GDP가 한국의 216%이지만, 이 회사 생산직 근로자를 보면 미국 직원은 한국 직원 급여의 64%만 받는다. 독일은 1인당 GDP가 한국의 180%인데, 영안모자의 독일 직원은 한국 직원 급여의 78%를 받고 있다.
미국과 독일 근로자의 임금 수준은 지게차 생산업체인 클라크의 창원공장과 비교한 것이다. 클라크 창원공장 근로자의 2012년 1인당 평균 임금은 6만2694달러(6580만원)였다. 지난해 1인당 GDP가 한국의 52% 수준인 브라질은 임금이 한국의 19%, 중국은 12%에 각각 그쳤다.
대우버스도 마찬가지다. 대우버스 울산공장 근로자의 지난해 임금은 5만9740달러(6270만원)인 반면, 중국은 한국의 14% 수준(8341달러), 카자흐스탄은 한국의 12%(7174달러), 파키스탄은 한국의 3%(1826달러)에 각각 그쳤다.
임금 수준이 높다 보니 동일제품의 생산 원가도 국내가 훨씬 높고, 판매 수익도 해외에 비해 낮다. 예를 들면 대우버스가 생산하는 BS106 차종을 울산공장에서 생산할 경우, 생산원가는 5만2731달러가 들지만 상하이(上海)는 한국의 90%(4만7211달러), 베트남은 91%(4만8044달러) 수준으로 줄어든다.
◇“강성노조 때문에 생산성 떨어지는데도 임금 상승은 계속되는 게 한국 제조업 현실”
원가 절감은 판매가를 낮추는 효과로 이어져 울산공장에서 생산한 차량의 90% 판매가격 수준으로 시장에 내놓을 수 있다. 그만큼 가격경쟁력을 확보할 수 있게 된다.
영안모자 대외협력 담당 문성훈 차장은 “국내 버스는 몇 년간 적자를 면치 못하고 있다. 원가를 10% 정도 줄이면 제조업 입장에서 큰 수익”이라고 말했다.
임금은 상대적으로 많이 받고 노는 날이 많은 것은 한국 제조업의 고질병인 ‘강성노조’가 가장 큰 원인이다. 예컨대 대우버스 노조의 경우 2008년 17일, 2009년 28일, 2010년 2일, 지난해 20일 등 최근 5년간 2011년을 제외하고 매년 파업을 벌였다.
2008년부터 지난해까지 파업 날짜는 총 67일, 매출손실액은 305억원에 달했다. 노조가 강성이다 보니 사측은 임금협상, 단체협상 등에서 노조의 요구를 들어줄 수밖에 없었다. 대우버스 노조는 2009년 초 구조조정에 반발, 사무직과 생산직이 함께 파업을 벌였고 사측은 구조조정안을 철회해야 했다.
생산성이 임금 상승을 따라가면 괜찮지만 적자를 보는 속에서도 임금 상승은 계속됐다고 영안모자 측은 밝혔다.
대우버스와 클라크 국내 공장의 경우 지난 10년간 사실상 적자를 기록했지만 근로자 임금은 매년 올랐다. 노조의 임금인상 요구를 들어주지 않을 경우 파업이 벌어지고, 그로 인한 손실이 더 크기 때문에 노조의 임금인상안을 수용해야 했다.
대우버스의 회계자료를 보면 2003년부터 지난해까지 10년간 474억원을 벌어들인 것으로 나오지만, 이 금액은 회사의 별도수입 811억원이 더해져 흑자로 둔갑된 결과다. 영안모자의 별도 자료에 따르면 최근 10년간 순수 버스 생산 및 판매로는 337억원이 적자였다. 같은 기간 해외 사업에서 347억원, 선물환 수입으로 383억원, 부동산 매각 등으로 172억원을 벌어 적자를 메울 수 있었다. 그럼에도 대우버스는 지난 10년간 매년 직원들의 임금을 올렸고 임금인상액을 모두 합치면 758억원에 이른다.
국내 인건비가 해외 법인보다 높은 건 복리후생비 비율이 높은 탓이 크다. 영안모자는 정기적으로 받는 임금과 성과금을 기본 급여로 책정하고 여기에 복리후생비를 더한 금액을 연봉으로 처리한다. 국내의 경우, 해외법인이 의무적으로 부담하는 항목 이외에 추가 지급되는 항목이 많았다.
예컨대 국내 대우버스 공장의 근로자 연봉이 총 5만9740달러라면 이 가운데 회사가 의무적으로 부담해야 하는 4대 보험 같은 복리후생비(9109달러) 외에 학자금, 식대, 선물대 등 해외에는 없는 추가 복리후생비가 2631달러나 됐다. 지난해 지급된 학자금은 15억5000만원이었다.
반면, 해외에선 4대 보험 등 의무적으로 부담해야 하는 조항 외에 별도 복리후생 명목의 부담금이 거의 없다. 중국 법인 등 몇몇 해외 법인이 식대와 주택부금 정도를 부담하고 있지만 금액이 적다.
◇“한국 제조업 살려면 국내 시장 대폭 개방해 물가 낮추고 노사문화 합리적으로 바꿔야”
백성학 회장은 “외국은 연봉을 정하면 그 외에 더 지불하는 게 없지만 국내는 인건비가 4만달러인 경우 기타 복리후생비로 30% 이상 추가비용이 든다. GDP 수준보다 높은 임금을 주다 보니까 경쟁력이 없다. 물가 때문에 급여를 GDP에 맞게 조정할 수 없다면 물가를 잡으면 된다. 우리 물가는 비싸다”고 말했다.
그는 “분야의 독점구조를 깨고 개방하면 물가를 낮출 수 있다”고 했다.
“밀가루 1㎏을 한국서 100원에 산다면, 해외에서 직접 수입할 경우 50원이 된다. 대만은 농업국가지만 50년 전 농산물을 개방하고 물가를 잡았다. 일본처럼 독점방식을 통해 운영되는 유통구조를 따라서는 곤란하다. 물가가 떨어지면 임금도 자연스럽게 조정될 수 있다. 고임금 구조가 지속되면 국내 제조업체들은 해외로 나갈 수밖에 없다.”
이런 국내외 임금 구조와 생산성 비교에서 역설적인 것은 해외에서 번 수익을 적자를 보는 국내 근로자들의 임금 인상에 쓰게 된다는 점이다. 영안모자를 비롯한 국내 제조업체들은 이를 ‘이익의 편취’라고 표현한다.
근로자들이 이런 편취에 상응하는 책임감을 갖고 생산성 향상 등에 노력해야 하지만, 국내 금속노조 산하의 제조업 지부들은 근로자의 급여와 복지에만 열을 올린다.. 강성노조로 인해 고용 유연성이 떨어지고, 직원들의 평균 연령이 계속 올라가는 현상도 해외 공장과 비교하면 뚜렷하다.
대우버스 울산공장 생산직 근로자의 평균 연령은 49.1세, 평균 근속연수는 23.3년이다. 반면 중국 구이린공장 생산직 근로자의 평균 나이는 40.7세, 상하이공장은 30.0세, 베트남 공장은 29.0세다.
영안모자의 한 관계자는 “국내는 호봉에 따라 매년 급여가 오른다. 해외 공장은 젊은 직원이 많고 급여도 상대적으로 적다. 국내 법인들은 적자가 나도 임금을 올리고 성과급을 주는 비정상적 경영을 한다. 노조는 스스로 자신들의 요구가 타당한지 여부를 살펴야 한다”고 했다.
물론 노조 측은 대표적 생산성 지표인 맨아워(man-hour)와 택타임(tact time)을 보면 한국의 생산성이 뒤지지 않는다는 주장을 펴고 있다.
맨아워는 근로자 1인의 시간당 노동량을, 택타임은 차체가 제조라인에 올라타고 완성될 때까지 걸리는 시간(분)을 각각 일컫는다. 실제 대우버스의 경우 연간 1인당 생산대수는 한국이 3.7대로 가장 높았고 중국 상하이 3.0대, 중국 구이린(桂林)은 2.2대, 카자흐스탄은 1.9대, 파키스탄 1.2대 순으로 나타났다.
지게차 택타임도 한국 창원공장이 16.8분인 반면 중국 칭다오공장은 26.1분, 멕시코 공장은 354분인 것으로 나타났다. 하지만 여기에는 ‘함정’이 있다는 것이 영안모자 측의 설명이다.
“단순 수치만으로 한국의 맨아워가 높게 보이지만 속내를 들여다보면 그렇지만 않다. 한국 공장은 자체 제작하는 부품이 없고 하청업체에서 납품을 받아 조립생산만 한다. 해외와 달리 금형화 시스템도 구축하고 있다. 해외 생산차종의 부품은 대부분 한국에서 만들어 가져가고 있다. 현지에서 조달할 수 있다면 맨아워를 줄이고 가격경쟁력을 더 높일 수 있다. 해외 공장은 구이린을 제외하고 대개 설립된 지 얼마 되지 않아 맨아워가 낮게 나오지만 점점 올라가고 있다. 이대로 가면 현대기아차처럼 해외 맨아워와 택타임이 국내 공장과 역전될 수도 있다.”
피부로 느끼는 생산성 하락은 뚜렷하다고 영안모자그룹 측은 말한다. 2003년 영안모자가 대우버스를 인수할 당시만 해도 울산공장의 신차 생산량은 1인 근로자 평균 1시간당 1대꼴이었지만, 지금은 10시간에 8대를 만들기도 벅찰 정도로 생산성이 후퇴했다고 한다.
이처럼 국내 생산성이 점점 추락할 경우 결론은 국내 공장을 포기하고 해외로 옮겨갈 수밖에 없는 것으로 압축된다. 모자 공장을 모두 해외로 옮긴 영안모자는 버스와 지게차의 국내 생산비중도 줄여가고 있다. 2010년 국내에서 생산한 버스는 총 3214대였으나 지난해에는 2721대를 생산해 15% 이상 줄었다.
반면 같은 기간 해외 생산비중은 25% 정도 늘어 총 3258대를 만들었다. 지게차도 2010년 국내에서 7400대를 생산했지만 지난해 6500대로 12%가 감소했다. 같은 기간 지게차의 해외 생산량은 168%나 늘었다.
영안모자 측은 현재 51%인 지게차 생산의 해외 비중 역시 2017년 85%까지 늘려 나갈 예정이다. 영안모자 측은 “몸집이 커진 국내 제조업체들은 대부분 해외로 공장을 옮겨가는 추세다. 국내 생산성을 제고하지 않는다면 이런 흐름이 계속 이어질 것”이라고 했다.
생산물량이 줄어드는 국내와 달리 영안모자 계열의 해외 공장은 활기가 넘쳐난다. 올 9월 기자가 직접 둘러본 대우버스 상하이 공장의 경우, 버스 생산 7년 만에 연간 1000대 정도를 제조하며 상하이를 대표하는 버스회사로 자리 잡았다. 상하이 시내 곳곳에서 대우버스 로고가 붙은 대형 또는 미니버스를 어렵지 않게 볼 수 있다.
2000만명의 인구를 가진 상하이시(市)에서 운행하는 버스 10대 가운데 3대는 대우버스다. 현지 직원들은 대우라는 브랜드 가치와 55년 간의 생산 노하우가 현지 착근의 원동력이 됐다고 말했다.
현지에서 만난 대우버스 남영구 이사는 “조만간 한국에서 생산 중인 1개 차종을 추가로 가져와 상하이에서 생산·수출할 것”이라며 “한국에서 상하이공장으로 생산라인을 옮긴 차량은 3개가 된다”고 말했다. 현재 상하이 대우버스 공장에서 만드는 차종은 초저상 시내버스, 수출용 일반버스 등 6개이다.
영안모자 측은 “노조를 없앨 수는 없지만 합리적인 방향으로 노사문화를 조성한다면 지금보다 최소 25% 이상 생산성을 올릴 수 있다고 본다. 잔업 등 급여를 올리기 위한 노조의 꼼수가 효율성의 발목을 잡는다”고 했다.
백성학, "생산성 하락 못잡으면 국내 제조업 무너진다"
photo 이경민 영상미디어 기자
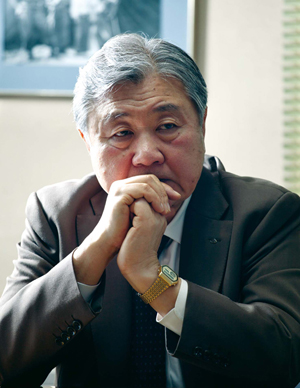
“국내 공장의 생산성이 해외에 비해 현저하게 떨어졌다”고 백 회장이 말할 때는 목소리가 올라갔다.
“기술력을 갖춘 기업은 해외로 나가야 한다. 국내 베이스를 적정선까지 유지하고 해외에서 번 돈을 한국으로 가져오는 구조가 이상적이다. 그런데 요즘처럼 등 떠밀려 나가는 건 곤란하다. 생산성 하락의 문제를 바로잡지 않으면 국내 제조업 기반은 무너지고 만다. 이런 상황을 뒤로한 채 경기가 호전되길 바라는 건 요행에 가깝다.”
백성학 회장은 1959년 영안모자를 창업한 이래로 54년간 모자, 버스, 지게차 등 줄곧 제조업만을 고집해왔다. 국내 제조업의 발전 과정을 몸으로 체험한 산 증인이다. 영안모자 계열의 국내 대우버스와 클라크 지게차 공장은 몇 년째 수익을 내지 못하고 있다. 해외에서 거둔 수익으로 국내 적자분을 메우거나 부동산 매각 등의 별도 수입으로 ‘무늬만’ 흑자를 만들어 왔다. 제조업 분야의 백전노장인 백 회장도 국내 공장의 생산성 추락을 막아내지 못한 것이다.
“인건비 비싸고 노는 날은 많고 노조는 툭하면 파업이다. 안타깝게도 그게 대한민국 제조업의 현실이다. 해외는 이런 문제를 고민할 필요가 없다. 에너지와 이자까지 싸다. 한국에서 공장을 운영하며 수익을 낸다는 게 어려운 일이 되어 버렸다. 해외 케파(생산능력)를 늘릴수록 돈을 더 버는 구조다.”
백성학 회장은 “생산성 저하로 인해 공장의 해외 이전은 피할 수 없는 흐름이 됐다”고 했다. 그러나 대한민국 기업이라면 국내 생산기지를 적정선까지 유지해야 한다는 게 그의 생각이다. 그래야만 해외의 돌발변수에 유연하게 대응하고 국가 발전에 일익을 담당할 수 있다는 입장이다.
“정치권과 노조가 생각을 바꿔야 한다. 정치인이 인기에 영합해 표를 가진 노동자 입장만 두둔하다가 생산성이 약화됐다. 게다가 국내 노조는 너무 강성이다. 내가 사업을 시작하던 해에 우리 국민소득이 79달러였고 지금은 2만2000달러를 넘어섰다. 무려 300배나 커졌다. 그러는 사이 허리띠를 졸라맸던 근성은 사라지고 생산성은 후퇴했다. 국가를 위해 또 기업을 위해 국내 제조업 공동화는 막아야 한다. 우리는 지금 어느 단계에 놓여 있는지 주변 국가와 비교해 봐야 한다.”
백성학 회장은 1993년 국내에서 모자 생산을 중단하고 해외로 진출했다. 국내로 다시 진입할 수 있었지만 600억원 규모의 시장에 세계 1위 모자업체가 진입한다는 게 적절치 않다고 판단했다.
그 대신 해외 판매망을 확대했다. 그는 대기업이 골목시장 상권을 위협하거나 하청업체를 쥐어짜는 관행을 버려야 한다고 꼬집었다. 그러면서 동시에 기업을 옥죄는 식의 경제민주화도 바람직하지 않다고 했다.
“1960년대부터 2000년대까지 한때 잘나가던 중소기업과 업종이 있다. 이 업체들은 이제라도 세계로 나아가야 한다. 예를 들자면 모나미 볼펜 한 자루가 절실한 나라가 얼마든지 있다. 그곳에 진출하면 우리 기업들은 성공할 수 있다.”
그는 현재의 기업 분류를 15단계로 세분화할 필요가 있다고 지적했다. “대기업·중견기업·중소기업으로 나누는 옛날 방식을 버리고 15개 정도로 넓게 기업을 구분해 각 기업군의 상황을 정확하게 파악해야 한다. 대기업 규제가 도입될 때 덩달아 철퇴를 맞는 중소기업이 생기는 일은 없어야 한다.”