현대에 오면서 인간과 자동차가 함께 보내는 시간이 점점 더 많아지고 소비자들의 요구사항에 따라 자동차는 첨단을 향해 달려간다. 이렇게 현대인에게 필요한 자동차의 생산공정은 어떻게 이뤄질까? 판넬을 성형하는 프레스 공장, 하나하나의 판넬을 용접, 조립하는 차체공장, 차체를 보호하고 아름답게 채색하는 도장공장, 각종 부품들을 조립해 비로소 움직이는 자동차로 완성하는 조립공장의 과정을 거친다.
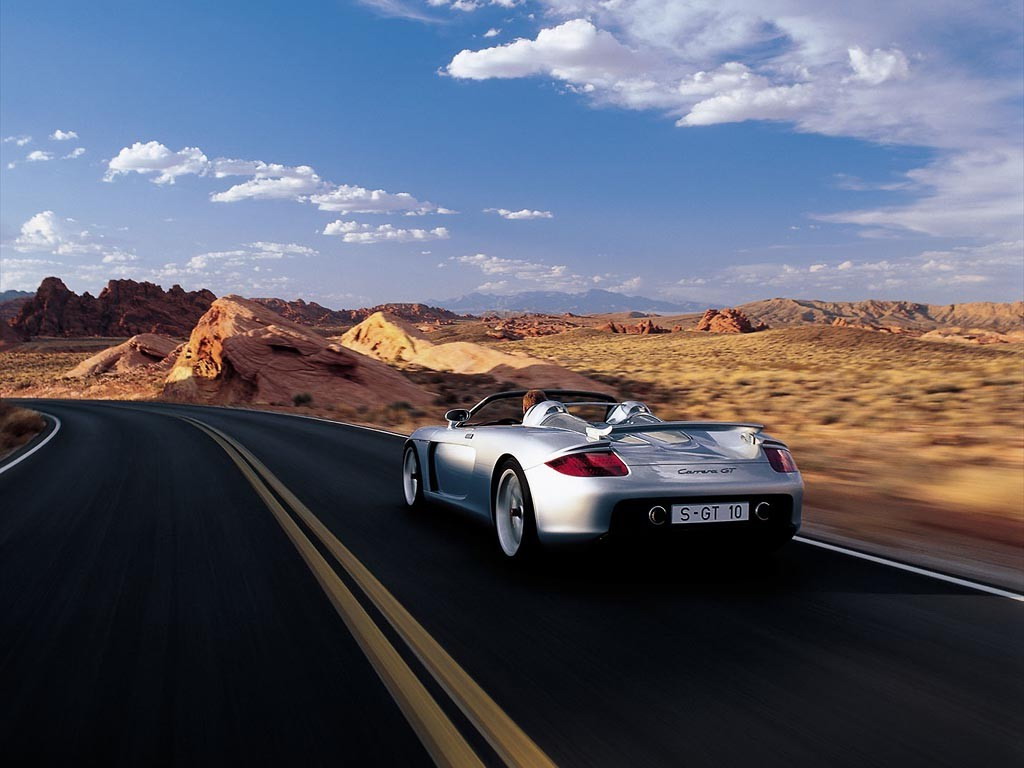
프레스 공장
프레스 공장은 자동차를 만드는 가장 첫 번째 공정이 이루어지는 곳이다. 마치 옷감을 재단해 옷을 만들 듯이 평면 상태의 철판을 금형과 프레스 기계를 이용해 자동차 각 부분에 필요한 입체적인 모양으로 만드는 작업을 한다. 주로 자동차의 스타일을 결정하는 문짝,지붕,바닥 등과 같은 크고 작은 판넬을 만든다. 이 낱낱의 판넬들이 차체공장으로 옮겨져 용접작업을 하면 차의 겉모양이 비로소 완성된다. 프레스 공장은 철판을 자르는 절단라인, 붕어빵을 찍어내듯 각 부위별 입체적인 모양으로 만드는 성형라인으로 구성된다.
절단공장-원형으로 둘둘 말려져 있는 자동차용 강판이 제철소로부터 프레스 공장으로 이동된다. 이 강판은 400여톤의 블랭킹 라인에서 각각의 필요한 부위에 알맞은 크기와 모양으로 잘라진 다름 수천톤의 프레스 기계로 눌러 지붕,문짝,차체바닥과 같은 입체적인 모양으로 만들어낸다.
성형공장-평면의 판넬을 여러 입체적인 모양으로 만들어 내는 성형공정은 트랜스퍼 프레스라는 기계가 작업을 수행한다.
트랜스퍼 프레스는 각각 3200톤, 2700톤, 1200톤, 800톤등 공정에 따라 다양하게 배치돼 있다. 이중 3200톤 프레스 기계에서는 앞 뒤 휀다, 엔진룸 덮개, 지붕 등 비교적 큰 부품을 생산하며 2700톤 프레스에서는 그보다는 작은 앞 문짝, 연료탱크 등을, 1200톤,800톤 프레스 기계로는 소형 프레스 물을 생산해 낸다. 한대의 프레스 라인에서 여러 종류의 프레스 부품을 생산하기 위해서는 생산하는 부품을 바꿀 때 마다 프레스 금형을 교환해야 하며 금형을 교환하기 위해서는 상당한 시간과 아주 힘든 노동이 필요하다.
따라서 작업자의 편의와 작업시간을 단축하기 위해 자동 금형 교환장치를 도입하기도 한다. 또한 이 트랜스퍼 프레스 기계들은 판넬 성형 시, 한번 성형된 판넬을 다음 성형공정으로 넘길 때 기계 스스로 알아서 옮기는 자동 이송장치가 있어 사람이 옮김으로써 일어날 수 있는 불량과 안정사고가 생길 수 있는 가능성을 최소화 한다.
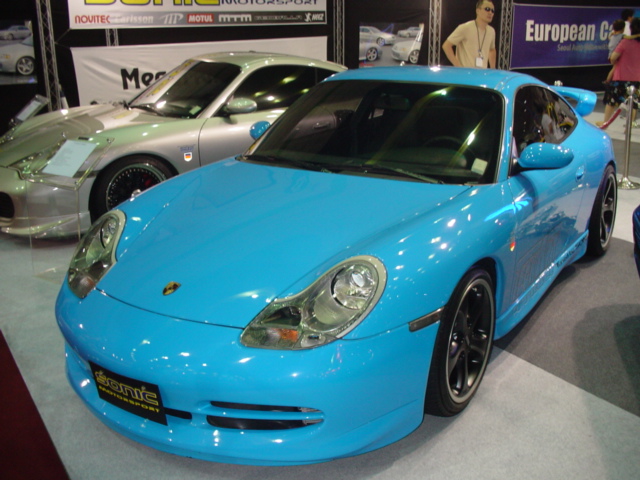
차체공장
수많은 공정에 걸쳐 성형된 판넬은 차체공장으로 옮겨져 용접,조립작업을 거쳐 차체로 완성된다. 차체공장에서는 프레스 공장에서 가져 온 낱낱의 패널과 외부에서 들여온 프레스 부품을 한데 모아 용접, 조립하여 차체를 완성하는데 이때 필요한 용접수를 모두 합하면 3600여점에 달한다. 이렇게 많은 용접을 사람의 손으로 일일이 할 수 없으므로 이곳 차체 공장은 230여대의 로봇을 설치해 둔다.
특히 국내 완성차 업체에서는 선진 자동차 기술인 IBS와 GRS 라인을 도입해 생산성을 극대화 시키기도 한다. 차체공장의 공정과정은 크게 3가지로 분류할 수 있는데 척째가 차게 바닥 만드는 곳, 둘째 차체 옆부분을 만드는 곳, 셋째 차체 중 여닫는 기능을 하는 부분 조립 등으로 작업이 이루어진다.
이중 차체를 조립하는 최초의 과정은 차체 바닥을 만드는 곳이다. 차체바닥은 엔진이 들어가는 엔진 룸과 사람이 앉는 좌성부분, 트렁크 부분 등 3부분으로 구성되어 용접로봇 80여대에 의해 용접 조립된다. 다음으로 차체 옆부분을 만드는 곳, 이곳은 문짝이 부착될 수 있는 차체 옆부분을 만드는 곳이다. 차체 옆부분은 문짝이 달리는 부분과 귀바퀴 위쪽, 즉 휀더 두 부분으로 구성되어 있다. 이렇게 조립된 부품은 다른 부품들과 함께 차체의 뼈대로 완성된다.
마지막으로 차체 중 여닫는 기능 부분을 조립하는 곳, 이곳은 차의 뼈대 부분이 완벽하게 용접된 차체에 보통 본넷이라 불리는 엔진룸 덮개, 문짝, 트렁크 덮개 등을 장착해 최종 완성된 차체를 만드는 곳이다. 외관 품질검사를 거친 뒤 완벽한 품질만을 골라 도장공장으로 옮겨진다. 특히 이곳에서 생산하는 부품들은 주로 차의 외관 구성하는 부품들이므로 자동차의 겉모습에 용접자국이 남게 되는 용접을 하지 않고 특수한 강력 접착제를 이용해 보기 흉한 용접 자국이나 흠집없이 깨끗하게 앞, 뒤판을 접착하는 방식으로 생산한다.
이렇게 꼼꼼하게 품질체크를 거친 차체는 자동 넘버링 장치에서 공정관리 시스템으로부터 컴퓨터를 통해 받은 차체 식별 번호 정보를 차체에 각인한 다음 엔진룸 덮개 앞문짝, 뒷문짝 등을 조립하고 외관품질을 거친 뒤 도장공장으로 옮겨 도장작업을 하게 된다.
도장공장
바디 공정이 끝난 차체는 충분히 세척을 한후 상, 중, 하 등 3-4회 도장을 하게 되는데 이때 불순물과 먼지로 인한 불량을 방지하고 도료 및 용제가스의 주변 확산을 방지하기 위해 완전 청결 밀폐된 부스내에서 도장 작업이 이루어진다. 도장공장의 공정을 순서대로 나열해보면 전처리-전착코팅-실링-언더코팅-드라이 생딩-중도-웨트샌딩-상도-폐인-페이트 피니쉬-리페어라인 순이다.
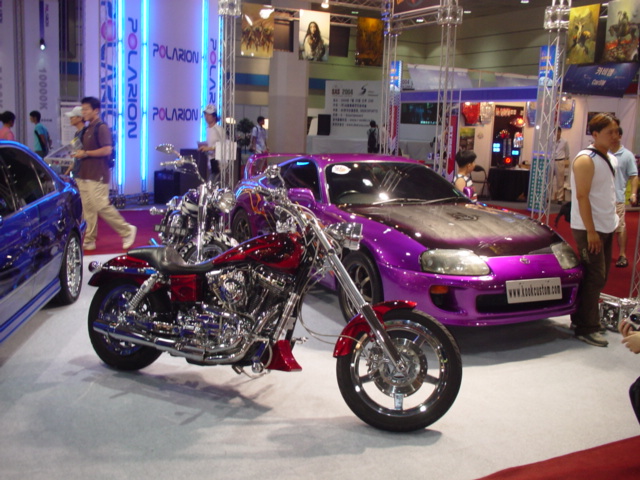
전처리 공정은 방청을 주목적으로 하기 위한 공정이다. 이곳은 차체 공장에서 차체제작 시 묻은 각종 오물이나 유지분을 깨끗이 세척하고 차체표면을 피막화성으로 처리하여 차체의 내식성 및 전착도료인 페인트의 부착성을 향상시키기 위한 공정이다.
전착 공정은 차체를 전착도료가 담긴 탱크에 완전히 담궈 외관은 물론 차체 내부까지 균일하게 도장하는 공정으로 방청성을 향상시켜 차체의 부식을 방지해 주는 매우 중요한 공정이다. 이외에 먼지와 부식방지를 위해 바디의 패널이 겹치는 부분 등에 방청, 방진, 방열을 목적으로 실러를 도포하는 실링 공정, 주행 시 소음과 진동을 부드럽게 하기 위하여 차체 바닥이나 도어 내부에 언더 코팅하는 공정등이 있다.
조립공장
조립공장은 프레스 차체 도장공장을 거쳐온 차체에 각종 부품을 조립해 달릴 수 있는 자동차로 완성시키는 곳이다. 작업순서는 우선 자동차에 필요한 전기를 공급하는 전기 배선류 를 설치한 뒤 엔진, 미션 등 동력을 전달하는 장치를 조립하게 된다. 마지막으로 나머지 부품들을 조립하고 브레이크 액 등 각종 액류와 가솔린을 넣은 뒤 완성차로서 기능을 잘 하는지 꼼꼼하게 검사하는 과정을 거친다. 합격된 제품은 주행시험장으로 옮겨 실제 도로를 달릴 대와 같은 여러 가지 상황에서 테스트를 한 뒤 완성차 대기장에 보관된다.
첫댓글 차가 너무 화려해서 차 보다가 내용이 기억안나는 관계로 다시 읽었어요..^^;;
도장작업이후의 특수 코팅 작업이 하나 더 생겼으면 하는 개인적인 바램. 도장작업이후 특수 필름( 투명과 다른 색을 구현하는 전자 장치의 반응에 의해 ) 을 차체에 부착하는 작업과 그이후 특수 코팅작업. 이런 작업이 공정상에서 실현되었으면 하는 바램이다.
우와~ 굉장히 전문적인 글이군요~ ^_^
좋은 게시물이네요. 스크랩 해갈게요~^^
좋은 게시물이네요. 스크랩 해갈게요~^^